The increasing use of multipurpose fill and finish lines means the dimensional control of prefillable cartridge packaging systems (nests) is more important than ever – to streamline pharmaceutical production processes and reduce waste.
Stevanato Group has built deep expertise in nest design over the years to effectively support customers with their new projects.
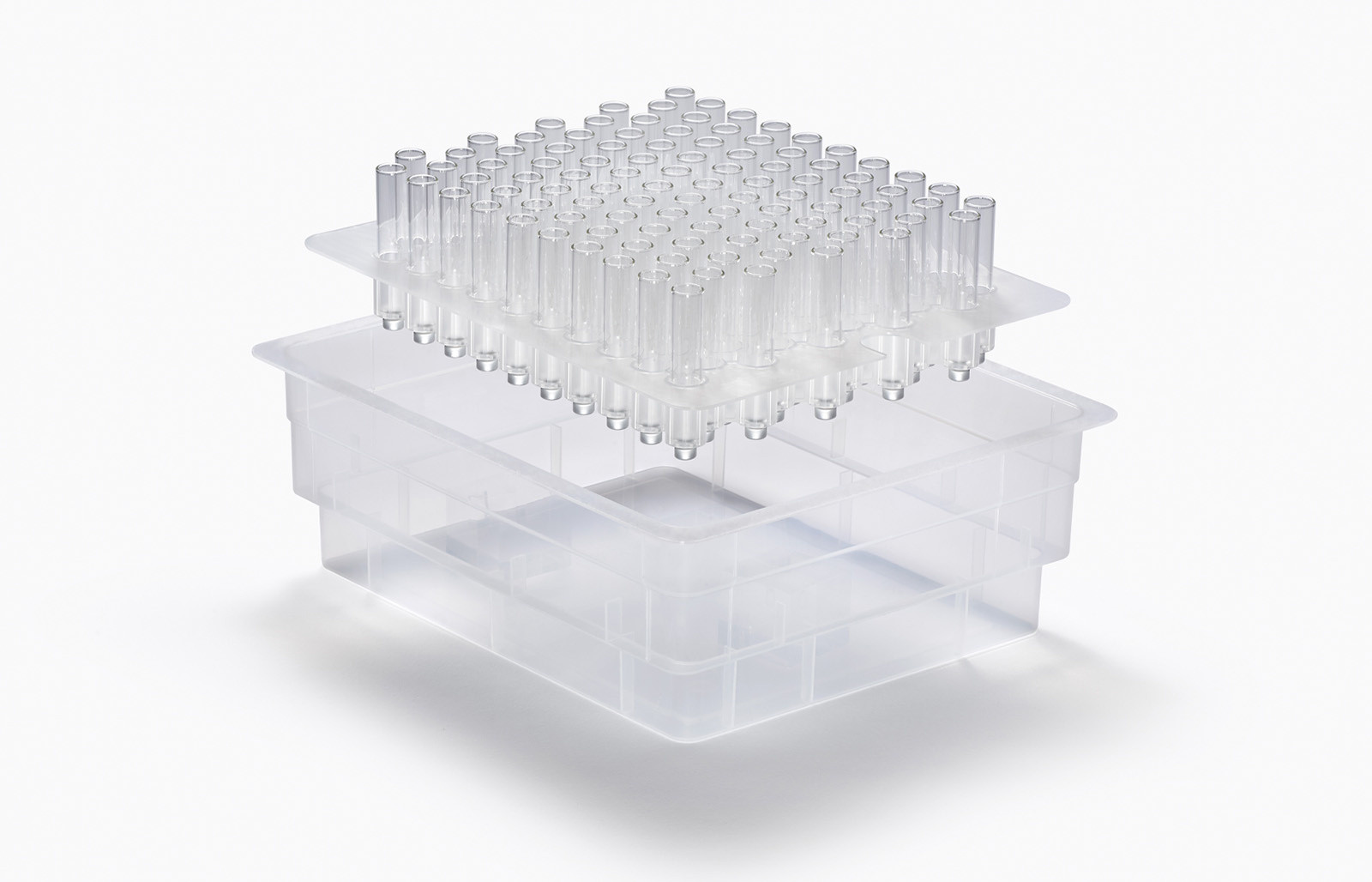
Opportunity
RTU cartridges undergo effective, fast and eco-friendly steam sterilization, which exerts thermal stress on the nest. The temperature of the plastic is raised to a point where the material characteristics are permanently modified. Optimizing this natural phenomenon is crucial to meet the dimensional control targets of ISO 11040-7 and guard against glass handling issues and potential breakages.
Methodology
Stevanato Group has carried out in-depth studies in collaboration with Crux to develop a numerical simulation model – combining fluid dynamics and thermal analysis – to predict the effects of steam sterilization. The aim was to optimize the process parameters for nest production and reveal which design would lead to the best performance.
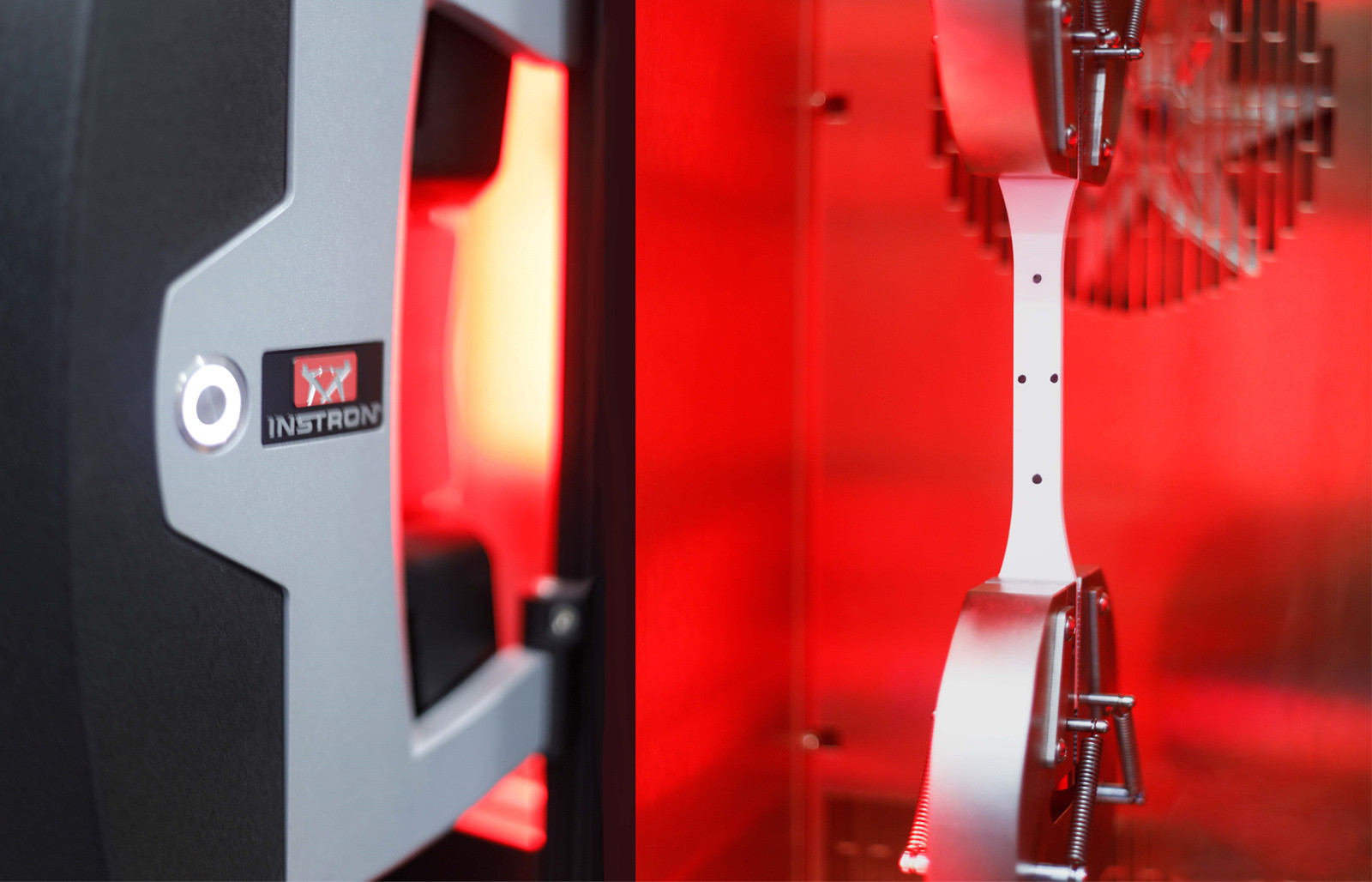
Figure: Measure instrument used to characterize materials in temperature.
A combination of material characterization, data analytics, and simulation was used to quantify the relative impacts of key process controls, such as injection molding temperatures and cooling durations. Moldflow simulations were combined with finite element analysis modeling to explore the behavior of the plastic during the cooling process.
The model was validated, ensuring that the numerical results were reliable and predicted what was experimentally observed. After model validation, the methodology was applied to several nests for steam sterilization – ensuring maximum performance during the product’s life, optimizing process parameters for nest production and enabling selection of the design giving the best performance.
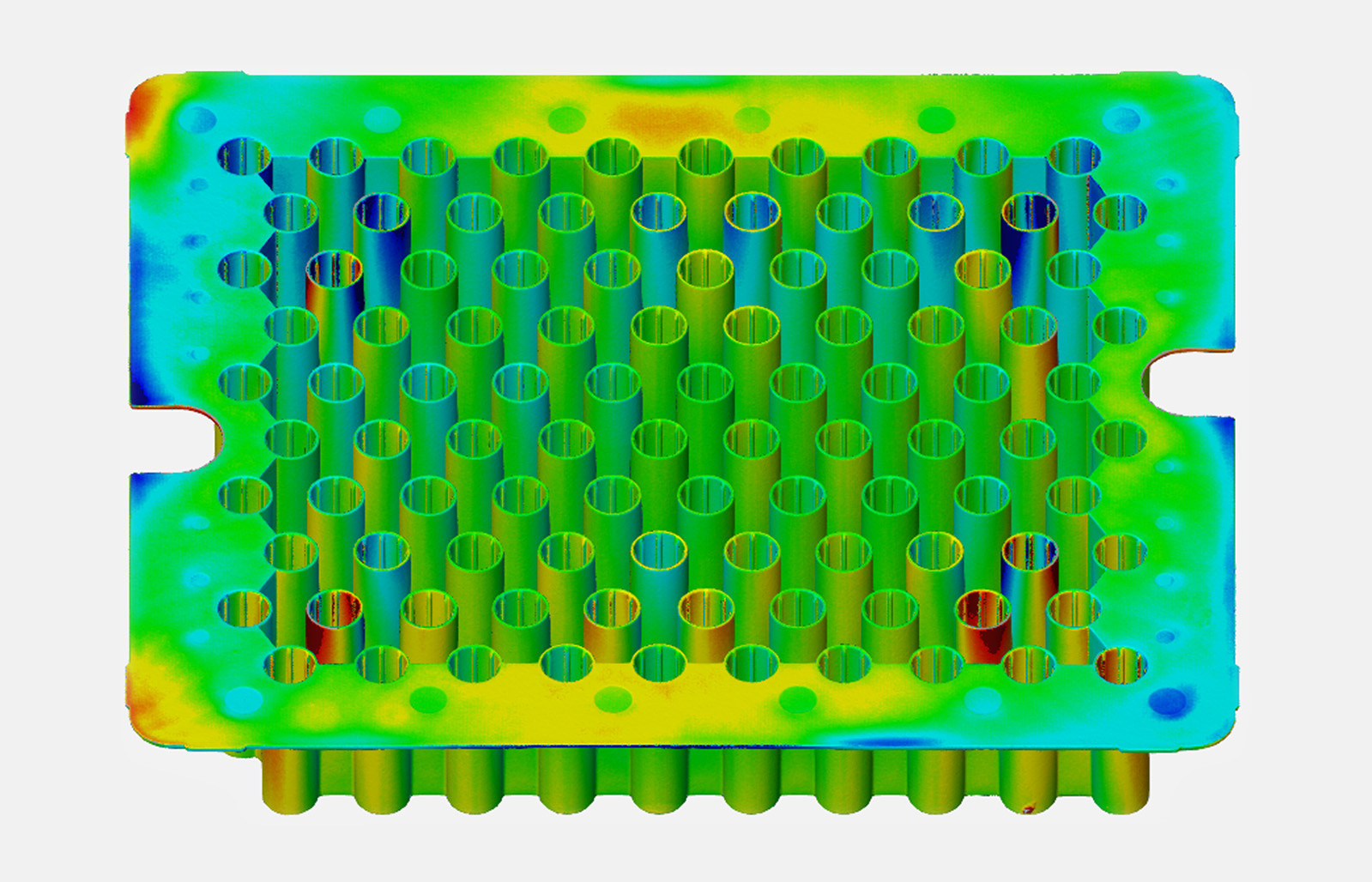
Figure: CT Scan showing areas of higher stress – most stressed areas in red.
Results
The study enabled Stevanato Group to maximize performance while optimizing polymer usage to improve sustainability.
The performance visible in the simulation results matched the measurements of the nests. The optimal nest design to minimize material changes could then be identified rapidly – without the need to produce several pilot molds. And the process parameters could be adjusted to ensure maximum performance.
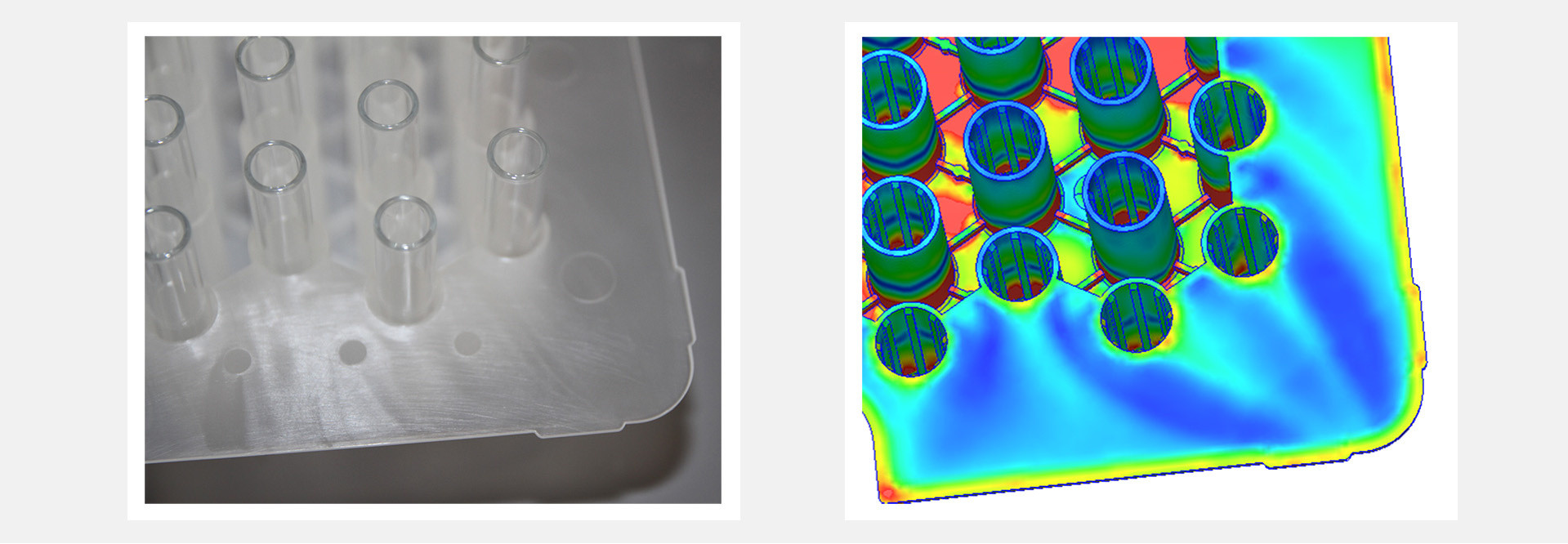
Figure: Image of a nest showing lines of flow (left) and numerical simulation (right). Areas of higher stress (darker blue) follow the pattern of flow lines.
Conclusion
- Robust validation of numerical model ensures reliable simulations –the method can easily be applied to different designs and materials.
- Stevanato Group can run these simulations for every new nest development to ensure rapid assessment of new designs and materials – leading to right-first-time solutions for rapid product development.
- Numerical simulation enables the comparison of different nest geometries to assess product performances.
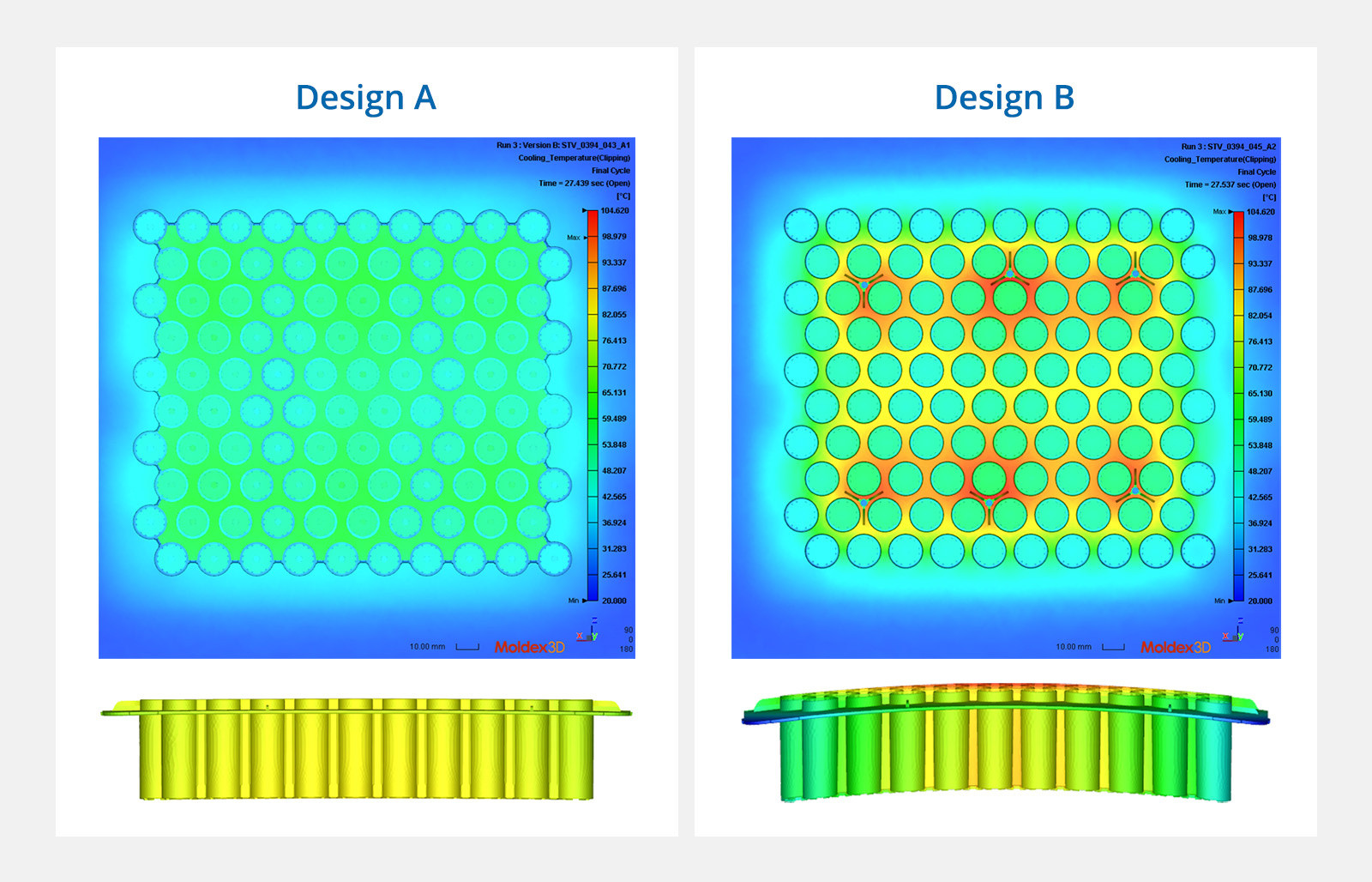
Figure: Comparison of two different nest configurations. The top view shows the temperature field in the nest mid-plane. The bottom shows a lateral view. The configuration on the left is optimal. Numerical simulation allows to identify the optimal configurations without the need to produce molds.
As a result, Stevanato Group’s work has two main benefits:
Reduction of time to-market through streamlined fill and finish processes thanks to prediction and reduction of natural material changes after the sterilization cycle.
Enhanced sustainability thanks to the optimization of polymer usage.
Author:
Chiara Mussoi, Product Manager Cartridge Platform
This article comes from a speech presented by Marco Longhin - Program Manager Drug Containment Solutions - in PDA Parenteral Packaging Conference, April 2023.
Figures: Courtesy of Crux.